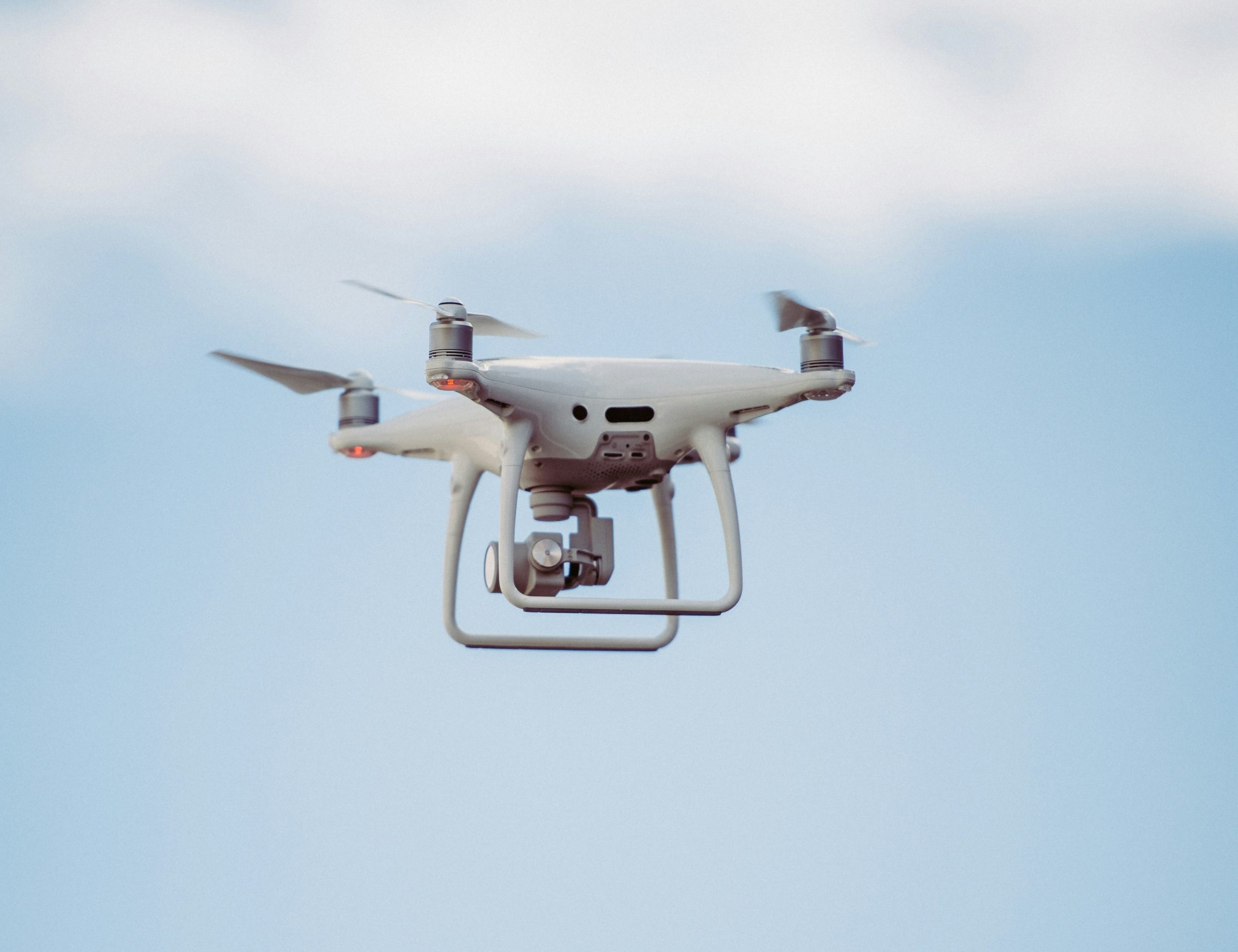
Designing advanced equipment requires a high level of precision, creativity, and technical understanding. With rapid technological advancements and the increasing demand for high-performance tools, the challenges in equipment design have become more complex. This article explores common obstacles designers face and practical solutions that help overcome these difficulties, allowing engineers and designers to produce innovative, effective, and reliable equipment.
Keeping Pace with Technological Advancements
One of the primary challenges in advanced equipment design is keeping up with the fast-evolving technology landscape. New materials, components, and techniques are constantly being developed, each promising to improve functionality, efficiency, or durability. While these advancements offer exciting possibilities, they also present challenges, as designers must continuously adapt and learn new technologies.
To overcome this challenge, designers should regularly engage in professional development and stay updated on industry trends through journals, conferences, and courses. Collaborating with experts from different fields can also enhance the design process, as interdisciplinary knowledge helps in leveraging emerging technologies effectively. For example, incorporating AI-based modeling can improve prediction accuracy in design, while new composite materials can reduce equipment weight and increase durability. By staying informed and flexible, designers can capitalize on technological advancements rather than being overwhelmed by them.
Balancing Functionality with Cost Efficiency
A critical aspect of advanced equipment design is finding a balance between functionality and cost. High-performance designs often involve specialized materials and complex manufacturing processes, both of which can drive up production costs. However, clients and companies typically seek cost-effective solutions while maintaining quality and functionality.
One approach to tackle this challenge is to focus on modular design. By designing equipment with interchangeable or replaceable components, designers can achieve both high functionality and reduced costs. Modular designs allow for easier upgrades and maintenance, extending the product’s lifespan and reducing the need for complete overhauls. Additionally, designers can use simulations and prototyping to test materials and optimize configurations, ensuring maximum performance with minimal waste. Leveraging cost-effective materials that offer high durability, such as advanced plastics, can further help balance performance and cost.
Managing Complexity and Reducing Design Errors
With advancements in technology and rising demand for multi-functional equipment, designs are becoming increasingly complex. This complexity introduces the risk of design errors, which can lead to functional issues or even equipment failure. Given that equipment must often meet strict safety standards, even minor errors can have significant consequences, making it essential to manage complexity carefully.
To address this issue, designers can incorporate iterative design processes that include multiple rounds of testing and refinement. Advanced simulation software, such as finite element analysis (FEA) and computational fluid dynamics (CFD), allows engineers to model and test equipment under various conditions before production, which can help identify and resolve potential problems early in the design phase. Additionally, breaking down complex designs into smaller, manageable sections or modules enables designers to focus on specific functionalities and ensure accuracy in each part. This modular approach not only simplifies the design process but also makes troubleshooting more accessible and more efficient.
Ensuring Reliability and Durability Under Varied Conditions
Equipment designed for advanced applications often needs to perform reliably under extreme or variable conditions, including high temperatures, heavy loads, and exposure to harsh chemicals. Ensuring that equipment can withstand such conditions without compromising performance is a crucial design challenge, as it requires careful material selection, testing, and sometimes incorporating protective features.
To achieve reliability and durability, designers should choose materials that are not only strong but also resistant to environmental factors like corrosion or abrasion. For instance, stainless steel and titanium alloys offer excellent durability, while certain plastics and composites provide resilience in chemically reactive environments. Incorporating rigorous testing protocols, such as thermal cycling or load testing, allows designers to observe how equipment performs under simulated real-world conditions. Adding protective coatings or seals to sensitive components is another effective solution to enhance durability, ensuring the equipment can endure various conditions while maintaining functionality over time.
Addressing User-Centered Design and Usability
In advanced equipment design, user-centered design (UCD) principles are vital to ensure that equipment is not only functional but also easy to use and maintain. Equipment that is difficult to operate or requires extensive training may reduce productivity and lead to operational errors. User-centered design addresses these issues by considering the end-user’s needs, preferences, and physical requirements.
Designers can address usability challenges by involving users early in the design process, gathering feedback, and conducting usability tests. Observing how users interact with prototypes can provide insights into necessary adjustments and enhancements. Employing clear visual cues, ergonomic controls, and intuitive interfaces helps simplify operations and enhances user experience. Furthermore, including clear documentation, labeling, and maintenance instructions can help users understand how to operate and care for the equipment, reducing downtime and improving productivity.
Advanced equipment design is a challenging yet rewarding field that requires balancing multiple factors, from technological advancements and cost efficiency to reliability and user-centered design. By understanding and addressing these challenges proactively, designers can develop solutions that push the boundaries of performance and innovation. The strategies discussed here offer practical ways to approach complex design challenges, ensuring that advanced equipment not only meets functional requirements but also excels in real-world applications. As technology continues to evolve, equipment designers who remain adaptable, informed, and user-focused will continue to succeed in creating high-quality, impactful tools.