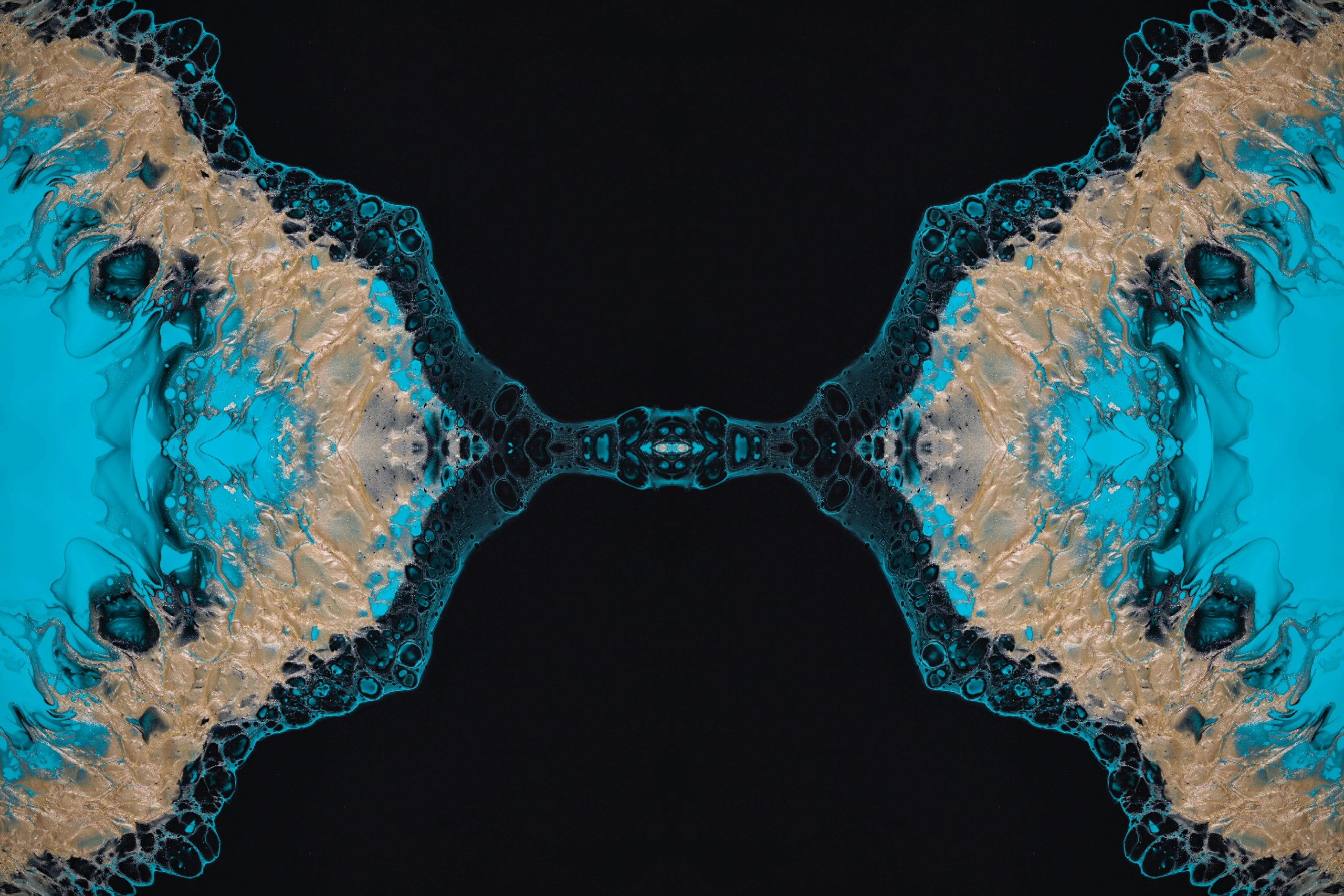
In the competitive landscape of industrial manufacturing, where efficiency dictates profitability, the role of catalysts is indispensable. Catalysts are used extensively across industries to speed up chemical reactions necessary for producing everything from fuels and plastics to pharmaceuticals and food products. While essential, catalysts degrade over time due to factors like poisoning, fouling, and thermal decomposition, leading to decreased efficiency and increased operational costs. Catalyst regeneration, a process where spent catalysts are restored to their original efficiency, emerges as a critical business strategy for maintaining profitability while adhering to environmental standards.
Decreasing Operational Expenditures
Catalyst regeneration is a cost-effective alternative to frequently purchasing new catalysts. New catalysts can be prohibitively expensive, and the costs associated with switching out a spent catalyst—including production downtime and the logistics of handling and disposing of hazardous materials—add significant financial burdens. Regeneration reduces these expenditures by restoring the active properties of catalysts at a fraction of the cost of replacement. This process can be integrated into regular maintenance schedules, minimizing downtime and enhancing overall production efficiency.
Prolonging Catalyst Life and Maximizing ROI
The ability to extend a catalyst’s lifespan through regeneration translates directly into an improved return on investment (ROI). By maximizing each catalyst’s functional life, companies can defer the capital expenses of replacement, allocating resources more efficiently and improving the bottom line. This extended lifespan also means that companies can achieve more consistent production levels and maintain product quality over more extended periods, which are crucial factors for customer satisfaction and market competitiveness.
Enhancing Energy Efficiency
Regenerated catalysts operate at optimal efficiency, ensuring that chemical processes consume less energy. Energy consumption is a significant cost factor in industrial operations, and reducing it through efficient catalyst operation can lead to substantial cost savings. Moreover, efficient processes result in fewer by-products and emissions, reducing waste treatment and disposal costs and mitigating environmental impact, which in turn aligns with global shifts towards sustainability and compliance with regulatory frameworks.
Leveraging Advanced Regeneration Technologies
The advancement of regeneration technologies has made the process more effective and accessible. Techniques such as chemical leaching, high-temperature calcination, and solvent extraction are tailored to address specific types of degradation, such as metal deposition, carbon build-up, or poison adsorption. These technologies not only restore catalysts effectively but do so with minimal risk to their structural integrity, ensuring that they can be regenerated multiple times without loss of efficacy.
Compliance and Environmental Benefits
Regenerating catalysts helps companies comply with stringent environmental regulations by maintaining the efficiency of the catalysts and thus reducing toxic emissions and waste. Compliance avoids legal penalties and reduces the risk of shutdowns or restrictions imposed by regulatory agencies. Furthermore, by promoting sustainable practices, companies can enhance their corporate image and appeal to environmentally conscious consumers and investors.
Competitive Edge in Market
Implementing a robust catalyst regeneration strategy can provide a significant competitive advantage. It demonstrates a commitment to innovation and efficiency, qualities that are highly valued in today’s market. Additionally, the cost savings and operational efficiencies gained from regeneration allow businesses to offer competitive pricing or reinvest in other areas of innovation, driving further growth and market expansion.
Strategic Implications
For businesses that rely heavily on catalyst-driven processes, regeneration should be a core component of their operational strategy. The economic benefits—ranging from direct cost savings and ROI improvements to compliance and market competitiveness—make catalyst regeneration not just a technical solution but a strategic imperative. As technology advances and environmental expectations rise, the ability to effectively regenerate catalysts will continue to play a critical role in the sustainability and profitability of industrial operations.
In summary, catalyst regeneration offers a host of financial benefits that can bolster a company’s bottom line while supporting sustainable and compliant operations. As such, it is an essential practice for businesses looking to thrive in the modern industrial landscape.