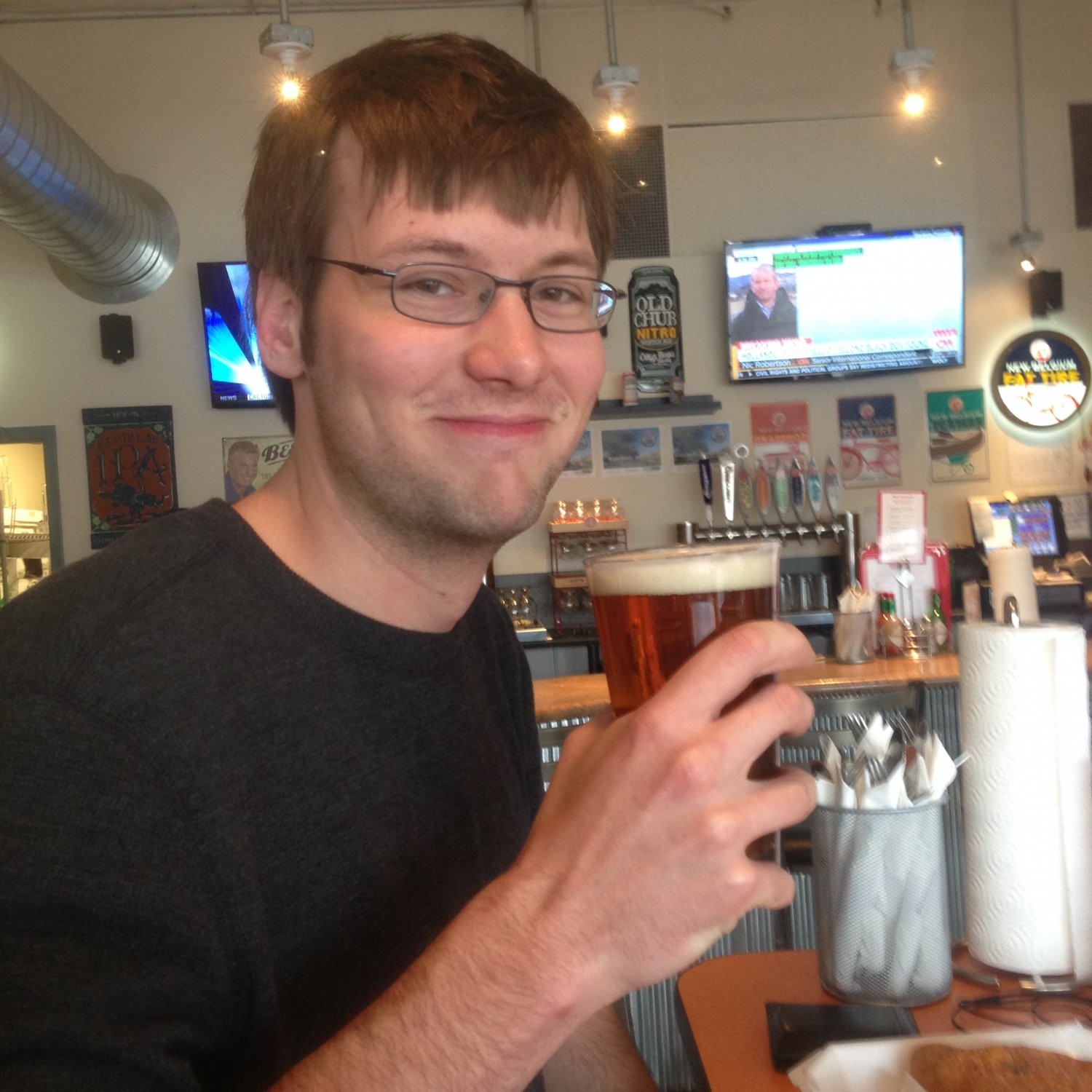
Branches of engineering play a crucial role in industries ranging from automotive to aerospace, energy, manufacturing, and beyond. At its foundation, mechanical engineering is built on several key principles that govern mechanical systems’ design, analysis, and operation.
Understanding these core principles is essential for any engineer working in the field, as they provide the basis for solving complex problems and creating innovative solutions. This article explores the fundamental principles of mechanical engineering that every engineer should master.
Thermodynamics and Energy Transfer
Thermodynamics is one of the most important principles in mechanical engineering. It focuses on studying energy, heat, and work and how they are transferred between systems. Engineers use thermodynamic principles to design energy conversion systems, such as engines, turbines, refrigerators, and HVAC systems.
First Law of Thermodynamics: This law, also known as Energy Conservation, states that energy cannot be created or destroyed; it can only be transferred or converted from one form to another. Engineers strive to minimize energy losses in the design of energy-efficient systems by applying this principle.
Second Law of Thermodynamics: This law introduces the concept of entropy and states that energy naturally flows from a state of higher concentration to one of lower concentration. It is crucial for understanding heat transfer, engine efficiency, and the limitations of energy conversion.
Thermodynamics is essential for optimizing the performance of mechanical systems, particularly those involved in energy generation, propulsion, and environmental control.
Fluid Mechanics and Hydrodynamics
Fluid mechanics studies fluids (liquids and gases) and how they move. It is another core principle that mechanical engineers use to design and analyze systems that involve fluid flow, such as pumps, pipes, turbines, and hydraulic systems. Engineers also apply fluid mechanics in aerodynamics design for aircraft, cars, and wind turbines.
The key concepts in fluid mechanics include:
Bernoulli’s principle states that as a fluid’s speed increases, its pressure decreases. This principle is crucial for understanding the behavior of airfoils in flight and the flow of fluids through pipes and pumps.
Viscosity: Viscosity refers to a fluid’s resistance to flow. Engineers must consider a fluid’s viscosity when designing systems to ensure optimal flow rates and avoid energy losses.
Laminar and Turbulent Flow: Laminar flow occurs when a fluid moves in parallel layers without disruption, while turbulent flow is characterized by chaotic, irregular movement. Engineers must understand these flow regimes to optimize fluid systems for energy efficiency and performance.
Fluid mechanics is critical in designing hydraulic systems, turbines, and air conditioning units, ensuring their efficient and safe operation.
Materials Science and Strength of Materials
Materials science is a fundamental area of mechanical engineering that focuses on understanding different materials’ properties, behaviors, and applications. Engineers must know how various materials respond to other forces, temperatures, and environmental conditions to select the appropriate material for a given application.
Strength of materials, also known as mechanics of materials, is the study of how materials behave under stress and strain. Engineers use this knowledge to design structures that can withstand loads without failing. Key concepts in the strength of materials include:
Stress and Strain: Stress is the internal force per unit area within a material, while strain is the deformation that occurs in response to stress. Engineers must ensure that materials can handle the stress applied to them without undergoing excessive strain or failure.
Elasticity and Plasticity: Elasticity refers to a material’s ability to return to its original shape after deforming. In contrast, plasticity refers to the permanent deformation of a material when subjected to stress beyond its elastic limit. Understanding these properties helps engineers design components that can withstand repeated loading without failure.
Fatigue and Fracture: Fatigue is the weakening of a material caused by repeated loading and unloading, while fracture is the breaking of a material due to stress. Engineers must account for these phenomena to ensure the long-term reliability of structures and components.
Key concepts in kinematics and dynamics include:
Newton’s Laws of Motion govern the relationships between forces and objects’ motion. Engineers apply these laws to design systems that move efficiently and predictably.
Velocity and Acceleration: Understanding the velocity (speed in a specific direction) and acceleration (rate of change of velocity) of moving objects is essential for designing mechanical systems that function safely and efficiently.
Torque and Angular Momentum: Torque measures the rotational force applied to an object, while angular momentum describes the object’s rotational motion. These concepts are particularly important in systems that involve rotating components, such as engines, turbines, and robotic arms.
Mastering kinematics and dynamics allows engineers to predict how mechanical systems behave under different conditions and optimize their performance.
Control Systems and Automation
In today’s increasingly automated world, control systems have become a critical area of mechanical engineering. These systems allow engineers to design machines and processes that can operate autonomously or with minimal human intervention. They are essential for modern manufacturing, robotics, and vehicle automation.
The fundamental principles of control systems include:
Feedback Loops: Control systems use feedback loops to monitor a system’s output and adjust the input accordingly to maintain desired performance. Engineers use feedback to ensure that systems operate consistently and accurately.
PID Control: Proportional-integral-derivative (PID) controllers are commonly used in control systems to maintain a stable output by adjusting input signals. Understanding how to tune a PID controller is essential for optimizing system performance.
Sensors and Actuators: Sensors measure various physical parameters (such as temperature, pressure, or position) and provide data to the control system. Actuators convert control signals into mechanical actions. Engineers must understand integrating sensors and actuators to design effective automated systems.
With control systems playing an ever-increasing role in modern industry, understanding the principles of automation is vital for any mechanical engineer.
These core mechanical engineering principles form the foundation of the field and are critical for solving real-world engineering problems. Whether working on energy systems, fluid dynamics, material selection, or automated control systems, mechanical engineers use these principles to design, analyze, and optimize various mechanical systems. Mastering these principles improves technical proficiency and enables engineers to drive innovation in industries that shape the world around us.