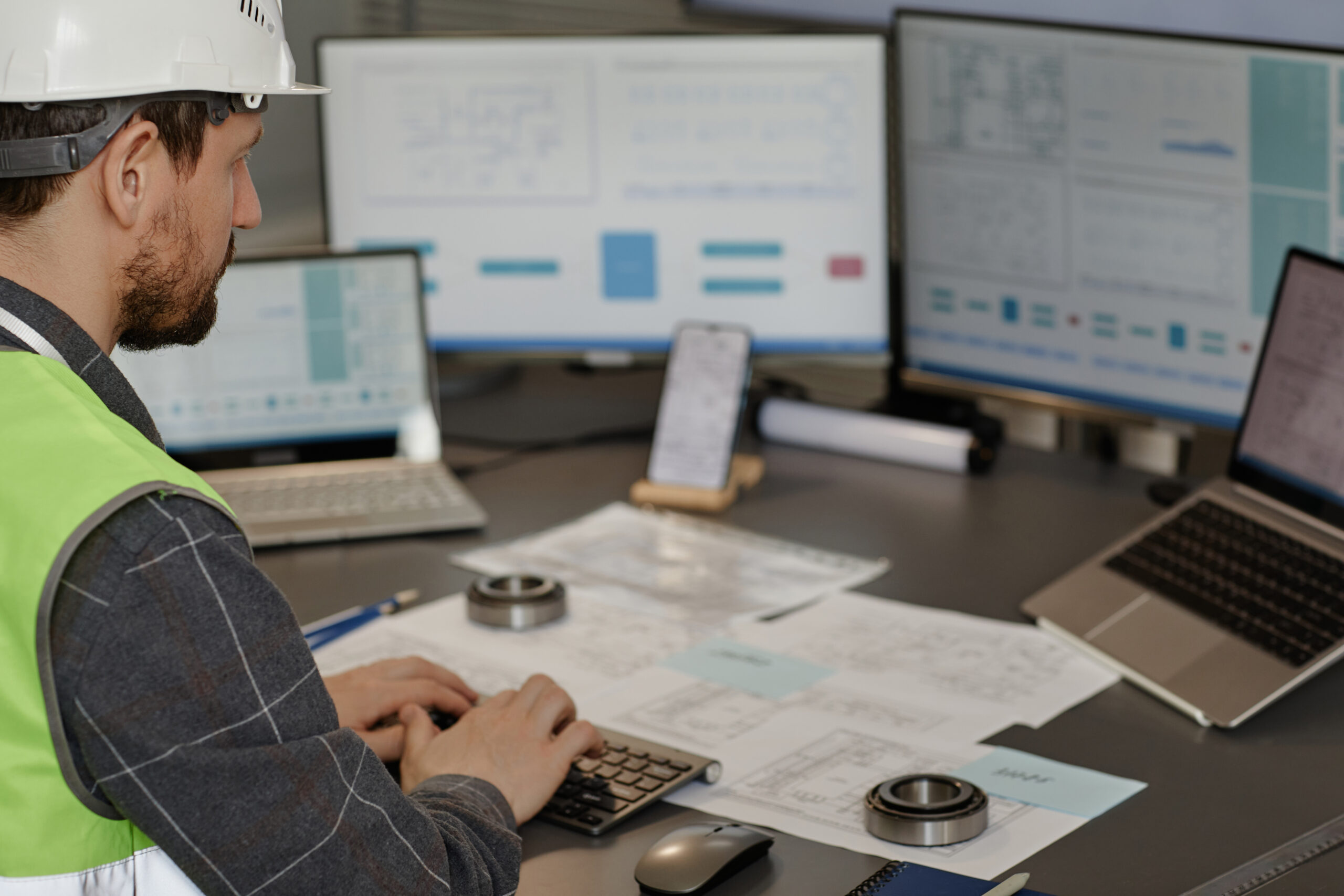
The design of advanced equipment is critical to modern engineering and technology. It encompasses a broad range of industries, including manufacturing, aerospace, healthcare, energy, and telecommunications, where the equipment needs to be efficient, reliable, and innovative. However, designing such equipment is not without its challenges. The complexity of modern systems, rapid technological advancements, and the increasing demand for sustainability present unique hurdles for engineers and designers. This article explores the key challenges faced in advanced equipment design and examines the innovative solutions implemented to address them.
Integrating Cutting-Edge Technology
One of the foremost challenges in advanced equipment design is integrating cutting-edge technology into a cohesive system. Technological change is accelerating, and designers often face difficulty incorporating the latest innovations into their equipment while ensuring compatibility with existing systems. Whether incorporating artificial intelligence (AI), robotics, machine learning, or advanced sensors, each new technology adds a layer of complexity to the design process.
To address this challenge, engineers are adopting modular design approaches that allow for easier integration of new technologies. Modular designs involve creating equipment composed of standardized components that can be easily replaced or upgraded as new technologies become available. This approach not only enhances the flexibility of the equipment but also allows for better scalability and future-proofing, ensuring that the equipment can evolve with technological advancements.
Additionally, advances in digital twin technology are being used to simulate equipment behavior before physical prototypes are built. Digital twins create a virtual representation of the equipment, allowing designers to test and optimize designs in a virtual environment. This simulation process helps identify potential issues early in the design phase, reducing the risk of costly errors during the production and operational stages.
Meeting Sustainability and Environmental Standards
As environmental concerns grow, sustainability has become a significant focus on advanced equipment design. Designers must now consider energy efficiency, material sustainability, and the overall environmental impact of their equipment. This is particularly relevant in energy, transportation, and manufacturing industries, where equipment often has a significant carbon footprint.
One key challenge is designing equipment that meets stringent environmental standards without compromising performance. For example, in the automotive industry, electric vehicles (EVs) are gaining popularity, but designing battery systems that are both efficient and sustainable is no small feat. Battery design requires balancing energy density, charging time, longevity, and cost, all while using sustainable materials and minimizing environmental impact.
To address this challenge, engineers are focusing on using renewable materials and improving the energy efficiency of their designs. Recyclable materials, such as aluminum and plastics, are becoming more prevalent in advanced equipment. In addition, designers are incorporating renewable energy sources like solar or wind power into the systems to reduce reliance on non-renewable energy.
Furthermore, companies are adopting circular economy principles, emphasizing the reuse, recycling, and repurposing of materials to minimize waste. The aim is to design equipment that operates efficiently, can be easily disassembled, and whose components can be reused or recycled at the end of its lifecycle.
Ensuring Reliability and Durability
Another significant challenge in advanced equipment design is ensuring the reliability and durability of the systems. Equipment used in critical applications, such as medical devices, aerospace systems, and industrial machinery, must be highly reliable and capable of withstanding harsh conditions over long periods.
Designing for reliability involves considering factors such as wear and tear, environmental conditions (temperature, humidity, vibration), and material fatigue. For instance, in aerospace engineering, equipment must endure extreme temperatures, high pressure, and vibrations while maintaining peak performance. Similarly, in healthcare, medical devices must operate reliably under continuous use in a sterile environment.
Designers use advanced materials with higher strength-to-weight ratios, corrosion resistance, and longevity to overcome these challenges. For example, aerospace applications increasingly use composite materials because they can withstand harsh conditions while remaining lightweight. Similarly, manufacturers carefully select biocompatible materials in medical devices to ensure both reliability and safety.
Another solution to enhance reliability is the use of predictive maintenance technologies. By integrating sensors and data analytics into the equipment, designers can monitor the system’s health in real-time. This data can be analyzed to predict when parts are likely to fail, allowing for preventative maintenance before issues arise, thus extending the equipment’s lifespan.
Managing Cost and Time Constraints
Advanced equipment design projects often face strict cost and time constraints, making delivering high-quality systems on schedule and within budget difficult. The complexity of modern equipment means that designing and testing new systems can take significant time and resources. Additionally, the cost of materials, labor, and specialized components can quickly increase.
To tackle these challenges, engineers are increasingly turning to design optimization techniques that allow for more efficient resource use. For example, computational design tools use algorithms to optimize equipment structure, reducing material waste while ensuring the system meets performance standards. These tools can help identify the most cost-effective design solutions by simulating various design options and analyzing their impact on overall cost and performance.
3D printing, or additive manufacturing, has also emerged as a valuable tool in reducing costs and production time. By allowing engineers to produce complex parts directly from digital models, 3D printing eliminates the need for expensive molds and tooling, significantly reducing production time and costs. Additionally, 3D printing allows for greater design flexibility, enabling the creation of customized parts that are optimized for specific applications.
Adapting to Changing Regulations and Standards
The regulatory landscape surrounding advanced equipment design constantly evolves, making it challenging for designers to keep up with changing standards. Regulations related to safety, environmental impact, and industry-specific requirements can vary greatly depending on the application and geographic location. Staying compliant with these regulations requires continuous monitoring and adjustment of designs, which can slow down the development process.
To address this challenge, engineers are utilizing more sophisticated regulatory compliance tools that streamline the process of staying up to date with changing standards. Using digital platforms that track and update relevant regulations, designers can ensure that their designs comply with the latest requirements. Additionally, companies are working closely with regulatory bodies and standard-setting organizations to help shape the future of these regulations, ensuring that the standards keep pace with technological advancements.
Another approach is the use of modular design, which makes it easier to adapt to new regulations. Designers can update specific equipment parts to meet new regulatory requirements without overhauling the system since modular components are standardized and easily replaceable.
Designing advanced equipment is a complex and multifaceted task that involves overcoming various challenges. From integrating the latest technologies and ensuring environmental sustainability to meeting stringent reliability standards and managing costs, engineers must navigate numerous obstacles to create efficient, reliable, and cost-effective systems. However, innovative solutions such as modular design, the use of advanced materials, predictive maintenance, and design optimization tools are addressing these challenges. As technology evolves, advanced equipment design will remain a critical area of focus, driving innovation and progress across a wide range of industries.