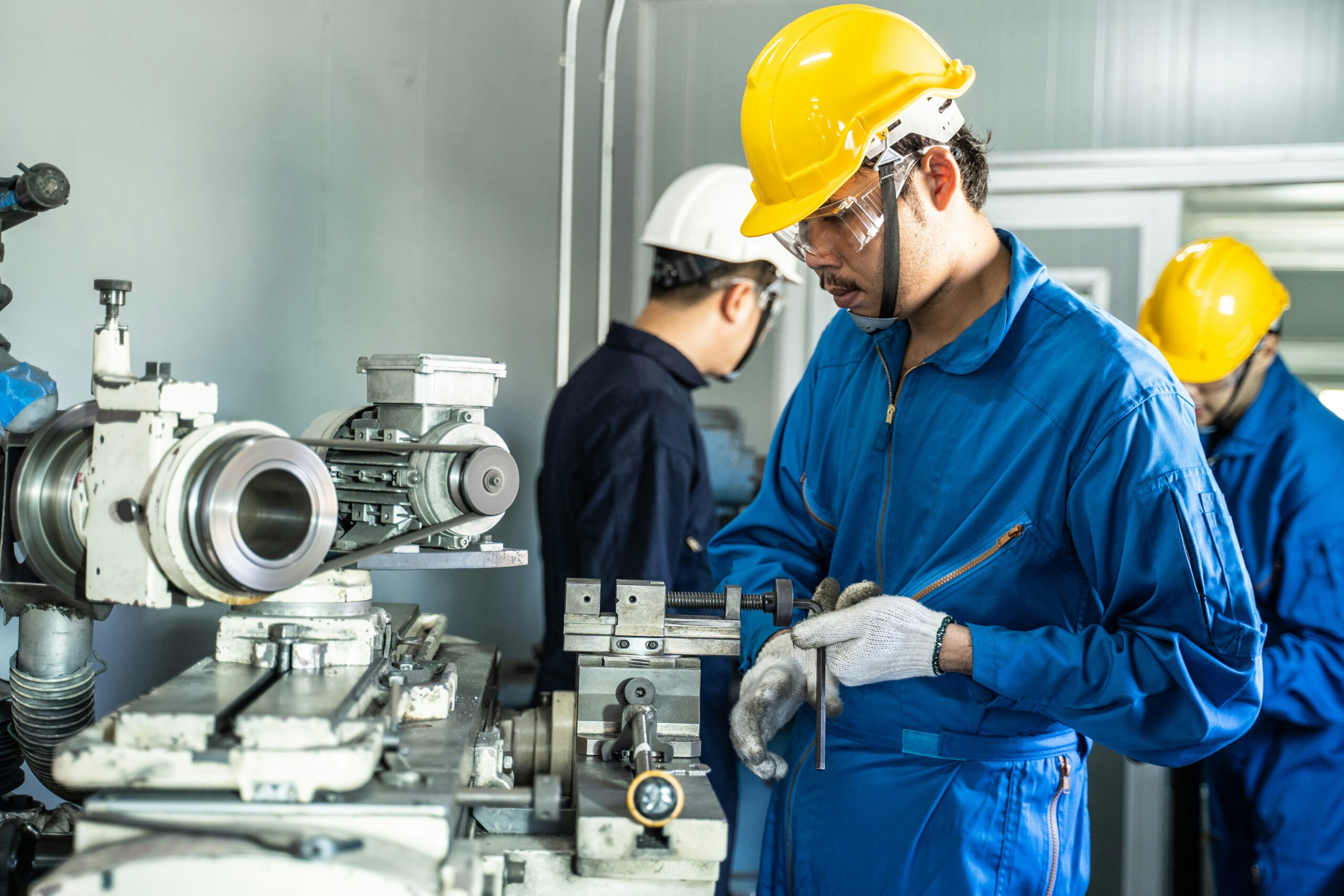
Mechanical engineering is built on carefully integrating theoretical concepts with practical applications. Engineers rely on a deep understanding of core principles such as thermodynamics, kinematics, and materials science to solve real-world challenges. Case studies in mechanical engineering illustrate how theoretical knowledge can be successfully applied to tackle complex problems, innovate within industries, and improve everyday life. These case studies provide valuable insight into the challenges and solutions engineers face while highlighting the role of collaboration, technology, and creativity in developing mechanical systems. By examining specific examples, we can better understand how mechanical engineers bridge the gap between theory and practice.
Understanding the Design and Application of Wind Turbines
Wind energy is a rapidly growing field in mechanical engineering, and the design of wind turbines offers a prime example of applying mechanical principles to a sustainable energy solution. The process begins with the theoretical understanding of aerodynamics, fluid dynamics, and thermodynamics to ensure that turbines can effectively capture wind energy and convert it into usable power. Engineers design turbine blades using the principles of aerodynamics, ensuring that the shape of the blades maximizes energy capture from the wind. This involves analyzing how air flows over the blades and how the shape influences the power produced.
However, theory alone is not enough to create functional wind turbines. The practical application of these designs requires a focus on real-world challenges such as material selection, structural integrity, and environmental impact. Wind turbines must withstand harsh weather conditions, including high winds and extreme temperatures. Engineers select materials that offer the right balance of strength and durability while keeping the turbines lightweight and cost-effective. Moreover, engineers must design wind turbines for easy maintenance and reliability to ensure they operate efficiently over long periods. The design and construction of wind turbines perfectly demonstrate how mechanical engineering principles are tested and refined in practice.
Advancements in Automotive Engineering: The Role of Thermodynamics
Thermodynamics is critical in automotive engineering, particularly in designing more efficient and environmentally friendly vehicles. Theoretical principles of energy conversion and heat flow are applied to improve the performance of car engines and reduce fuel consumption. In a conventional internal combustion engine, thermodynamic laws govern the conversion of chemical energy into mechanical energy, which powers the vehicle. Engineers utilize the principles of thermodynamics to optimize engine efficiency by minimizing energy losses due to friction, heat dissipation, and exhaust gases. Engineers achieve this by designing more efficient combustion chambers and improving the heat management systems in the engine.
In practice, applying thermodynamics to automotive engineering goes beyond theoretical calculations. Engineers must also consider the practical challenges of manufacturing and assembly. For example, using new materials like lightweight alloys and composite materials helps reduce the overall weight of vehicles, leading to better fuel efficiency. Moreover, engineers heavily rely on thermodynamic principles to integrate hybrid or fully electric drivetrains, ensuring that energy from the battery is used effectively. Engineers must also account for the real-world conditions a vehicle will operate in, such as varying driving speeds and environmental temperatures. Through iterative testing, design optimization, and applying thermodynamic principles, automotive engineers can create vehicles that perform better and are more energy-efficient.
Robotics and Motion Control: Real-World Applications
Robotics offers an exciting field where mechanical engineering principles come to life in machines that perform tasks precisely and efficiently. The theory of kinematics, which describes the motion of objects without regard to the forces that cause the motion, is fundamental in designing robots that can move in a controlled manner. Engineers use kinematic models to create robotic arms, legs, and other appendages capable of performing tasks such as picking up objects, assembling parts, or assisting in surgery. By understanding how the joints and links of a robotic system move relative to one another, engineers can create robots that function accurately and consistently in various environments.
In practice, the design and deployment of robots require a deeper understanding of dynamics and control systems. Robotics engineers integrate sensors, actuators, and feedback systems to enable robots to adjust their actions based on real-time data. For instance, a robot in a factory setting may need to change its movements based on the size, weight, and orientation of the parts it handles. Dynamic modeling allows engineers to predict how robots respond under different conditions, ensuring they operate smoothly and safely. Additionally, selecting materials and integrating efficient power systems are critical for ensuring that robots can perform tasks over extended periods without overheating or breaking down. This combination of theoretical knowledge and practical considerations illustrates the role of mechanical engineering in developing highly functional robotic systems.
The Application of Fluid Dynamics in HVAC Systems
Heating, ventilation, and air conditioning (HVAC) systems are another area where mechanical engineering principles, particularly fluid dynamics, are crucial in solving real-world problems. HVAC systems rely on the movement of air and refrigerants through ducts, coils, and compressors to control temperature, humidity, and air quality in buildings. Fluid dynamics principles help engineers design these systems to ensure the efficient flow of air and refrigerant while minimizing energy losses. By understanding the principles of fluid flow, engineers can optimize the layout of ducts and piping to reduce resistance, prevent leaks, and maintain the required airflow and pressure throughout the system.
Beyond theoretical calculations, engineers must also consider practical challenges such as space limitations, cost, and energy efficiency when designing HVAC systems. For instance, engineers must design HVAC systems in large buildings or industrial applications to handle high volumes of air and refrigerant without taking up too much space or requiring excessive energy. Engineers use advanced simulation tools to model fluid flow and optimize the design of HVAC systems for specific applications. In practice, achieving the right balance between system size, efficiency, and cost requires careful consideration of the materials used in ducts, fans, and compressors. By applying fluid dynamics principles and considering real-world conditions, engineers can design HVAC systems that provide optimal comfort while reducing energy consumption.
The Integration of Automation in Manufacturing
The integration of automation has revolutionized manufacturing processes, and mechanical engineering plays a crucial role in developing automated systems that perform repetitive tasks with speed and accuracy. The theoretical principles of mechanical systems, such as force transmission, motion control, and materials handling, are essential in designing machinery that can automate complex manufacturing tasks. For instance, engineers design robots on assembly lines to handle parts with great precision, using actuators and motors that rely on mechanical engineering principles to move parts, weld, or apply coatings.